Climate and Paper Technical Brochure
Discussions about the effect of climatic influences during storage and transport and in the process of printing and finishing are as old as the industrial production of paper itself. Generations of experts have had to deal with the more pronounced negative effects and there are numerous publications in the field of specialist literature on measuring temperature and humidity
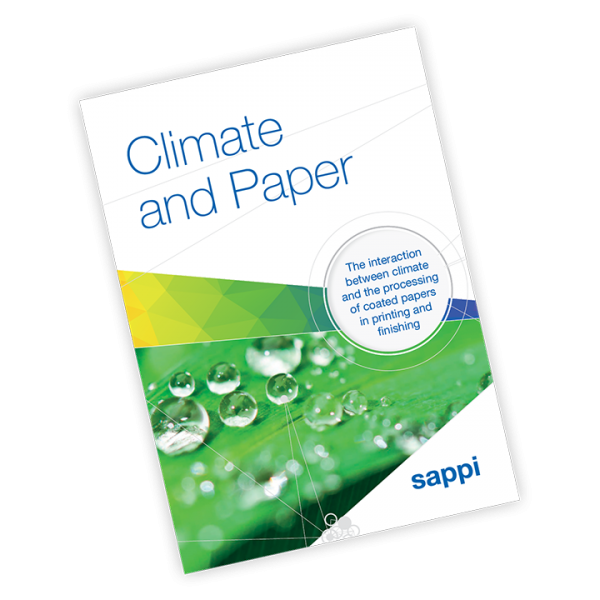
Generally speaking, there are few climate related problems in printing and finishing. As a result, climate only becomes an issue when printing problems occur, such as dot doubling, misregistering, creasing or curling. Obviously, the likelihood of this happening, is more pronounced in seasons with extreme weather conditions, such as hot summers and cold winters. In these periods, improper handling – unwrapping the paper prematurely, use of paper that is too cold – or unfavourable conditions in the printer’s or binder’s facilities, can have disastrous consequences for the flatness and runnability of the paper.
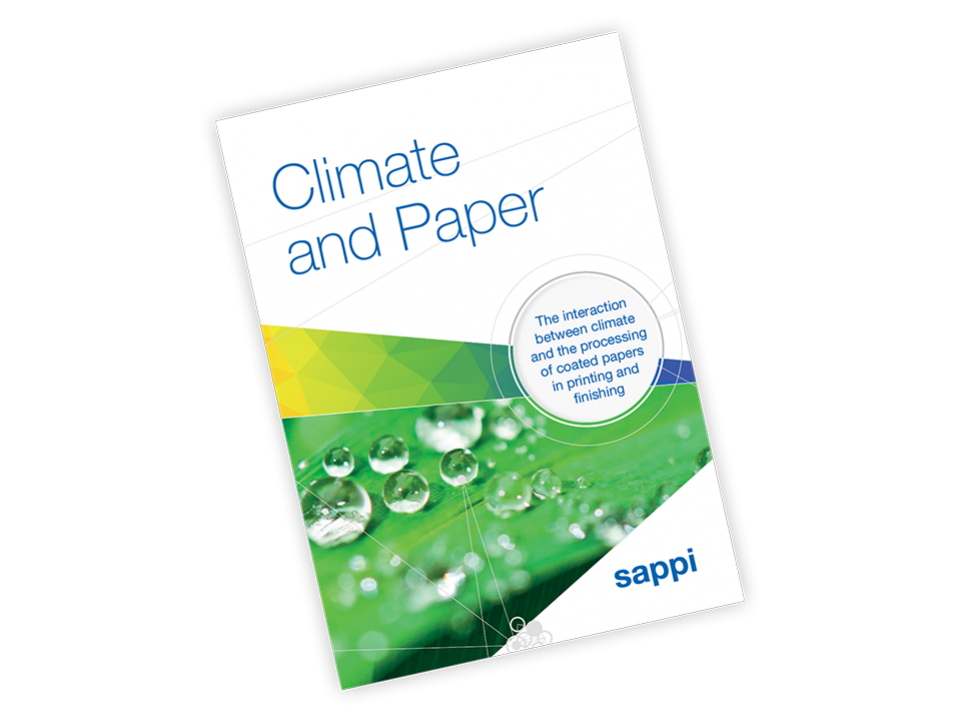
What will I find inside this technical brochure?
This publication is intended to help clarify some of the more serious negative effects of climate circumstances. It offers guidelines for correct handling of coated papers, one of the pre-conditions for optimal control during the actual process of printing.
Contents:
- Chapter 1: Introduction
- Chapter 2: Definition of terms
- Chapter 3: The influence of interior climate on paper flatness
- Chapter 4: The relation between climate and technical printing problems
- Chapter 5: Circumstances within the printer's power of control
- Chapter 6: Special issues in web offset printing
- Chapter 7: Problems in web offset printing
- Chapter 8: Measuring temperature and humidity
- Chapter 9: Sustainability
Get a sneak peak of Chapter 3 below.
Chapter 3: The influence of interior climate on paper flatness
The influence of air humidity
Production problems can occur in offset printing when the paper has certain deformations, either in the form of wavy edges or tight edges. The reason why these phenomena cause so much trouble, is the full contact between blanket cylinder and impression cylinder in the printing zone, where these deformations can lead to dot doubling, misregistering and creasing.
Wavy edges occur when the humidity of the sheets of paper in the stack is below that of the surrounding air, in other words, when excessively dry paper is subjected to average, but inevitably higher air humidity, or when normally humid paper is subjected to extremely high air humidity. This will predominantly be the case during the hot and humid months of summer in non-conditioned warehouses and printing premises, or when damp proof wrapping is not used during transport or storage in humid conditions. On the other hand, if too cold and already unpacked paper is introduced into the warm air of the printing shop during winter, the surrounding air temperature will sharply drop, thus causing a sudden rise in air humidity. The edges of the sheets will absorb moisture, making them swell in relation to the centre of the sheets. The result is wavy edges.
Tight edges occur when sheets of normally humid paper are subjected to exceedingly dry air humidity. In this case, moisture is absorbed from the edges of the sheets, which, as a result, shrink in relation to the centre. This will mainly occur during winter, when the relative air humidity in heated, non-conditioned or non-humidified working spaces can drop to levels as low as 20% of the normal values. Usually, damp proof wrapping provides efficient protection against humidity influences. Obviously, to be able to offer such protection, the wrapping must be completely intact.
Deviations in humidity balance of up to 5% in either direction do not lead to wavy edge or tight edge effects. At a difference in relative humidity of 8-10%, however, the situation quickly becomes critical.
The influence of interior temperature
Temperature has only minor effects on the humidity of a stack of paper. Nevertheless, temperature remains an issue to be reckoned with, since it is one of the elements determining relative air humidity. This means that, in case of an observed difference in stack temperature and room temperature, the paper should remain wrapped in its damp proof packaging until this difference in temperature has been evened out. The time this takes will vary in individual cases and will depend on the extent of the temperature difference and the size of the stack. The graph below contains general guidelines.
Direction in which moisture is absorbed by or exuded from the stack of paper
Tight edges occur when sheets of normally humid paper are subjected to exceedingly dry air humidity. In this case, moisture is absorbed from the edges of the sheets, which, as a result, shrink in relation to the centre. This will mainly occur during winter, when the relative air humidity in heated, non-conditioned or non-humidified working spaces can drop to levels as low as 20% of the normal values. Usually, damp proof wrapping provides efficient protection against humidity influences. Obviously, to be able to offer such protection, the wrapping must be completely intact.
One thing to keep in mind is that different types of paper have different properties of heat conductivity. Therefore, temperature balancing times can also vary with different paper types.
The influence of humidity on curling tendency
The tendency to curl is closely connected to fluctuations in humidity. Curling is caused by the paper fibres expanding and shrinking in the cross direction. When paper is moistened on one side, the fibres expand in one direction, causing the paper to curl toward the dry side. As soon as a balance in humidity within the paper structure has been restored, the effect is cancelled out – unless this is prevented by uneven fibre distribution.
The influence of stack humidity and temperature on ink drying
Exceedingly high humidity balance of the paper stack can lead to significant extension of ink drying times. Experience shows that stack humidities of up to 60% do not cause drying times to rise significantly. Above 60%, however, the effect is very much pronounced, and in some cases leads to drying periods three times as long as normal.
Relation of temperature balancing time and difference in temperature and stack size
Extended drying times can also occur when the stack of printed paper is too cold. When printed paper is temporarily stored in a cold room (temperature dropping from 25 to 5°C), the ink will take 10-15 hours longer to dry.